Before the manufacturing process starts, a lot of preparation needs to be done. It needs to be selected carefully to meet high standards regarding veins structure, humidity, time of year the tree has been cut down, all sorts of risks of showing cracks, deformation, deseases, etc.
Once chosen the wood you can not start immediately. You need to be patient for the wood needs to be dried out before setting off.
1- CHOOSING THE WOOD

Usually for the shaft, a soft type of wood like the North-American ash or maple is being chosen. Regarding the back part of the cue a harder and heavier tropic type of wood (e.g. ebony) is being selected.
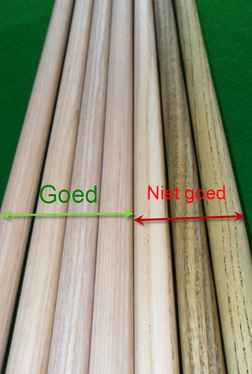
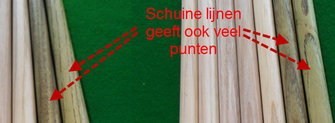
We all know what a wooden board can do after being exposed to humidity or variation of temperature. This goes as well for a snooker cue. So electing the wood in its initial fase requires knowledge and experience. Out of a mass of 1 cubic meter planks of wood probably only 10% will pass the first test to meet quality demands.
It is an absolute priority that veins are running straight. The more veins wood contains, the more veins the cue will show on the outside. The straighter the veins to the first 40 to 50 cm of the shaft, the better the response of the cue while cueing.
Also color is important. Its color should be light and equal. Dark staines in the wood are an indication the wood is not meeting healthy requirements sufficiently, and eventually the cue will react different by this.
2- DRYING THE WOOD
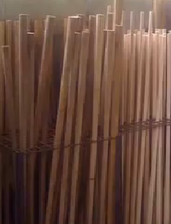
Wood lives! So before setting off to become a final product it needs to be dried out completely so that substances are eliminated. There are different techniques used for this.
A long term drying is used by stacking wood outside in a shed, enabling air to pass through. The artificial way of drying wood goes a lot faster. Here wood is being exposed to high temperatures in drying ovens or with heating elements. Moisture and substances within will evaporate much quicker.
Avoiding all kinds of hazards during the process, the drying process of the wood, selected by our web cue doctor, will vary in time between 1,5 to 2 years; depending on the type of wood. Hard wood needs more time to dry than soft wood.
3- STADIA OF MANUFACTURING
It all starts with a large block-shaped piece of wood measuring 5 by
5 cm. During the following months it is kept on room temperature to see if cracks appear. When it is approved for further processing, the first drying process will take 2 months. Should the wood
bend there is no need for alarm. It will run its first time through the cutting machine to extract the bend.
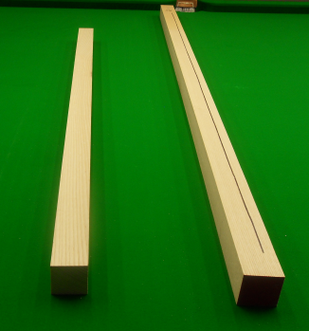
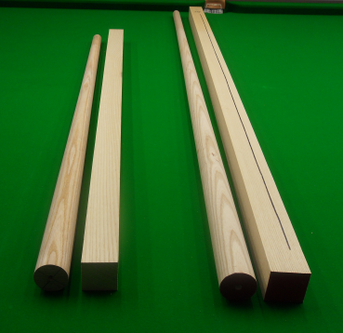
And then everything starts over anew. A few months drying to see how it will respond and further bending will be eliminated through the cutter again. With each process the wood becomes thinner and thinner. The process is being repeated until the wood has dried out completely and stopped from bending.
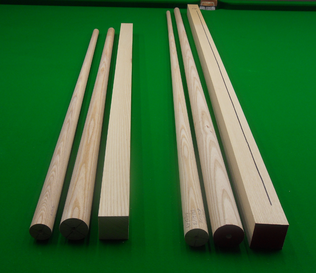
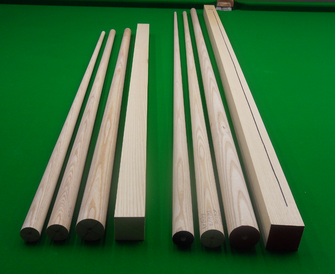
Why can we not shape the wood to its final size immediately? Should the wood bend after we finished it, there is nothing we can do anymore. This piece of wood can not be used as a cue. And that is final. But isn’t it possible to counterbend it with heating? Yes you can counterbend it. But usually a piece of wood will go through drying and cutting processes several times to get rid of serial bends. Using the method of heathing to counterbend it repetitively, finally will not leave us with a perfect straight cue.
So, when the cue still is displaying bends after having reached its
minimum diameter through different cutting processes, the cue can not be used anymore. There for initially it is really important to be very careful choosing the best fitting wood for this
job.